The process entails four steps:
1) Printing
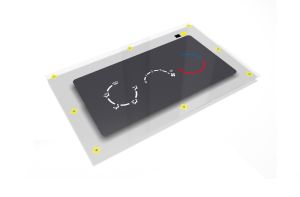
All common methods of printing (such as screen printing) but also more specialized methods (such as thermosublimation) may be used. In the case of transparent films (such as PA) the design is usually printed on the backside to protect it from scratching. However, translucent films or opaque films (such as ABS) are also employed in which case the design or decoration is applied from the top.
The colors used in printing should be especially suited to the FIM process. Please contact us for more information on the right selection.
2) Thermoforming
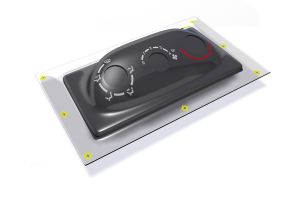
The printed film is converted into a 3D shape. The most common method is vacuum deep drawing but high pressure forming (HPF) is also recommended for high-quality articles (especially embossed films) to achieve outstanding precision and reproducibility.
If the article to be processed has a flat shape, this step may be left out.
3) Stamping
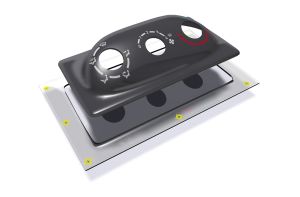
The printed and formed film preform is now stamped out of the film. This preform already has the geometrical properties of the future injection-molded part.
4) Injection molding
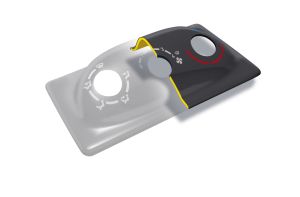
The preform is now placed into the cavity of a mold tool and fixed in place. After closing the two halves of the tool, the liquid polymer melt of the injection mold material is pressed into the shape. Upon solidification the melt bonds with the printed film. To achieve optimal adhesive strength, selecting the right types of printing ink and adhesive agent is crucial!
Especially PP, ABS, ABS/PC, PC but also high-quality polyamides, such as PA12 are used as injection molding materials.